U příležitosti 30. výročí firmy připravil Warwick, německý výrobce stejnojmenných baskytar a kytar značky Framus, speciální nadílku pro všechny příznivce čtyř a více strun. Uspořádal týdenní Bass Camp, první ročník série workshopů s těmi nejlepšími hráči, kteří používají jeho nástroje, a zároveň uspořádal den otevřených dveří, kdy dal široké veřejnosti možnost nahlédnout do tajů výroby jedněch z nejproslulejších nástrojů moderní éry. I my jsme měli možnost podívat se takříkajíc „za oponu“ a v následujícím textu se pokusíme tento pohled zprostředkovat i vám.
„Hlídka“ Music Store nebyla v prostorách firmy Warwick poprvé, od naší návštěvy před zhruba sedmi lety se však mnohé změnilo. Pozměnil se proces výroby, přibyly unikátní výrobní technologie, které především přispívají k mnohem větší preciznosti i ekologičnosti. Našimi průvodci v markneukirchenském sídle byla Nina Hoschkara, ve firmě zodpovědná za komunika-ci s tiskem, a také muzikant a skladatel Andy Irvine, který již léta úzce spolupracuje s tímo německým výrobcem. Protože Warwick v posledních letech začal vyrábět také v asijských zemích, kam přesunul produkci běžných sériových modelů i zesilovačů Warwick a Framus, došlo v továrně v Německu k jedné zásadní změně: Dnes se zde vlastně vůbec nevyrábí běžné sériové modely, ale prakticky pouze jen špičkové modely v malých sériích a z převážné části především zakázkové, takzvané Custom Shop nástroje vyrobené na bázi základních modelů s detaily, které si určují sami zákazníci, tedy baskytaristé a kytaristé, kteří chtějí nástroj značky Warwick či Framus vyrobený podle vlastních specifikací.
Custom Shop nabízí celou řadu možností, které umožňují nechat si zde vytvořit nástroj přesně podle vašich představ. Ten potom bude sice tvarem vycházet z existujících modelů Warwick, můžete si však podle svých představ zvolit nejen materiály a povrchovou úpravu, ale také různé detaily, jakými jsou například druh použitých ladicích mechanik, profil a konstrukce krku či konkrétní snímače nebo elektronika.
V poslední době výrobce zapracoval také na své nabídce kytarových modelů, a nabízí tak celou škálu variant i pro milovníky šesti, ale také sedmi strun, ať už běžných elektrických kytar, nebo jazzových hollow-body nástrojů. Přímo v Markneukirchenu pracuje téměř sedmdesát (a to včetně pracovníků v kancelářích a skladech) z celkových několika stovek zaměstnanců. Přímo ve výrobě je jich zapojeno něco přes dvacet.
Celá továrna sice nepůsobí dojmem monstrózního kolosu, stále je to spíše středně velký podnik, nicméně jak odhalily její útroby, jedná se o ukázku nejmodernějších a v řadě kroků i zcela unikátních výrobních procesů a technologií, které umožňují výrobu nástrojů s celou řadou jedinečných vlastností, kterých si oko na první pohled možná ani nevšimne. Svědčí však o nich celá řada patentů, které výrobce v baskytarách Warwick a kytarách Framus používá. „Je pouze jediná továrna na světě, jako je tato, nikde jinde ve světě takovou nenajdete, a to z mnoha a mnoha důvodů.“ zdůrazňuje na začátku více než půlhodinové exkurze Andy Irvine. Proto dáme i vám nahlédnout, jak vypadá opravdu moderní výroba špičkových nástrojů. Dlužno však podotknout, že vše není zdaleka jen dílem vyspělých, přesných strojů. Jak jsme se přesvědčili, finální podobu dávají nástrojům zručné ruce zdejších nejlepších pracovníků – vždyť právě kvůli nim se celá firma před několika lety přestěhovala právě do Markneukirchenu, do kraje, kde dříve na druhé straně hranic s Českem dlouho vyrůstala tradice výroby hudebních nástrojů v Lubech a Kraslicích. „Jsme hrdí na to, že prakticky poloviční část stavby nástrojů provádíme ručně,“ chlubí se Andy Irvine.
Sklad dřeva
Dřevo je jednoznačně základ nástroje. Celá prohlídka tak začíná v rozlehlé otevřené hale, kde do výšky několika metrů ční naporcované a logicky seskládané a pečlivě přířezy označené nejen podle druhu, ale i podle letopočtu. Pro zde vyráběné nástroje má Warwick v zásobě poměrně velké množství dřeva, které nakupuje v podobě základní suroviny – celých kmenů, které jsou až v továrně rozřezány na polotovary používané k výrobě. Už při nákupu je tedy nutná velká zkušenost, která nákupčímu firmy umožní rozpoznat třeba jen podle fotografií kmenů očekávanou kvalitu dřeva.
Byl by to ráj pro každého kytaráře. Najdete tu prakticky jakékoliv dřevo, jaké se dnes používá k výrobě kytar a baskytar od tradičního javoru, jasanu, palisandru a ebenu, až po méně obvyklé druhy, jako je v současnosti stále oblíbenější bubinga, extrémně tvrdý snakewood, který se používá například pro hmatníky signature modelu Steva Baileyho a mnoho dalších. V zadní části skladu najdete také první zásoby dřeva označeného certifikátem FSC, který garantuje jeho původ z legální těžby v šetrně obhospodařovaných lesích. „Do budoucna bychom se na dřevo certifikované FSC chtěli orientovat stále více, ale není to úplně snadné. Každý kus musí být zvlášť označený, což celý proces zároveň i prodražuje.“ říká nám k tomu Nina Hoschkara. V úhrnu má podle ní továrna k dispozici zhruba něco mezi 40 až 50 druhy dřevin, započítáme-li mezi ně i speciální dřeva vyznačující se výraznou kresbou, která jsou určená především pro Custom Shop modely. Do výroby se používají kusy, které venku přirozeně schnou pět až patnáct let. Ve skladu ale najdete také materiál starý třeba přes dvacet let, příkladem je třeba 26 let staré třešňové dřevo, z něhož je vyrobena výroční limitovaná edice modelu Streamer. To vše si s sebou Hans-Peter Wilfer přivezl do Markneukirchenu z Bavorska, kde svou továrnu provozoval dříve. Dřevo je již ve skladu rozděleno podle směru let na samčí a samičí a označeno tak, aby se při výrobě správně kombinovaly kusy se shodnou strukturou. Platí, že směr let nesmí jít při konstrukci nástroje proti sobě.
Cesta dřeva ze skladu pokračuje přes jednu ze dvou sušiček, kde se jeho vlhkost dostává na požadovanou úroveň. „Optimální vlhkost dřeva, které jde do výroby, se pohybuje mezi 7, 6 a 9 procenty. Na vzduchu přitom může dojít přirozeným vysycháním k poklesu maximálně na 14 procent, na požadovanou vlhkost se tedy dřevo dostane až v sušičce.“ připomíná Nina Hoschkara. Ve vakuové sušičce trvá sušení dva, tři týdny, šetrnější „soft“ sušička dřevo suší pozvolna pět až šest týdnů.
V továrně
Kolem sušiček vstupujeme do samotných výrobních prostor. Po prvotním rozřezání prochází dřevo vstupující do výroby nejprve kontrolou vlhkosti a kusy, u nichž je její úroveň pod nebo nad požadovanou normou (tj. pod 7, 6, nebo nad 9 procent) jsou označeny červenou či zelenou čárkou a dřevo je automaticky podle této hodnoty rozděleno. V prostoru haly je vlhkost rovněž kontrolována, takže pokud je příliš nízká, začnou vám speciální trysky nad hlavami rozprašovat mikrokapičky vody, která postupně dostane vlhkost na patřičnou úroveň a z prostředí ji absorbuje i samotné dřevo. V opačném případě se dřevo vrátí zpět do procesu sušení. Už samotný krok měření vlhkosti je první zárukou kvality a stability. Umožňuje, aby byly k sobě použity adekvátně vyzrálé kusy dřeva, které takříkajíc nepůjdou proti sobě. Má to význam nejen u těl lepených ze dvou kusů, ale zejména u krků, které jsou dnes u většiny baskytar, ale i kytar vyráběny kvůli vyšší stabilitě z více kusů. Následně po opracování dřeva na hoblovacím stroji probíhá selekce dřeva. „Náš specialista na dřevo pečlivě vybírá jednotlivé kusy tak, aby se k sobě hodily a doplňovaly se, měly určitou synergii, která se projeví v charakteru nástroje.“ popisuje Andy Irvine. Díky tomu například u těla ze dvou kusů odpovídá jak kresba při pohledu na horní stranu, takže tělo vypadá téměř jako z jednoho kusu, tak také souhlasí směr let při pohledu z profilu. Kombinace označené modrou šmouhou pak konečně vesele putují do výroby.
V další fázi probíhá na speciálních strojích, v podstatě na speciálně navržených lisech, samotné lepení těl a krků. Tlak, pod nímž je k sobě dřevo lepeno, je přitom tak velký, že je posléze vrstva lepidla prakticky neviditelná. „Pro modely Streamer, jejichž tělo je z horní i spodní strany klenuté, se tělo lepí ze dvou kusů už pod patřičným úhlem, což je úspornější z hlediska dřevěného odpadu.“ říká Andy Irvine.
Pro krk se u většiny modelů používá laminovaný materiál slepený z více (podle šířky a konstrukce krku ze tří, pěti, nebo i sedmi) kusů dřeva, obvykle dvou druhů. V tom případě se pak kombinují samčí a samičí kusy. „Krk z jednoho kusu dřeva je jen tak silný, jako toto dřevo, pokud slepíte krk ze tří kusů, jeho pevnost, odolnost proti mechanickému namáhání a životnost krku vzroste až desetkrát. Kombinace dvou kusů, jejichž léta směřují v úhlu 45 stupňů a jednoho kusu s rovnými lety, který je vsazen mezi tyto dva, vytváří prakticky nezničitelný krk.“ vysvětluje Andy Irvine. Proto se mimochodem krky z více kusů používají i u importovaných modelů z Asie.
Právě u krků je skvěle patrný šetrný přístup k využití dřeva. Jelikož většina modelů má zkosenou hlavu, je základní laminovaný blok či hranol připraven vlastně pro dva krky – na obou koncích dojde k seříznutí zkosení pro hlavu v patřičném úhlu a odřezky se použijí pro nalepení jako „uši“ po stranách hlavy na každém konci. Následuje nalepení plátů s logem „W“ tvořícího povrch hlavy, vyfrézování výřezů pro výztuhy – uprostřed s nastavitelnou dvoucestnou výztuhou (u baskytar, u nichž je tah strun velký, se ještě po stranách nachází dvě kratší drážky pro dva vnitřní ocelové pláty zvyšující stabilitu krku). Po instalaci výztuh jsou na každou stranu nalepeny hmatníky. Za zmínku stojí patentovaný přístup k matici výztuhy, který je chráněn speciální odklápěcí krytkou. Teprve poté je celý blok rozřezán na dva kusy, z nichž vzniknou dva krky.
Po těchto přípravných fázích jsou polotovary připraveny pro klíčovou fázi – frézování v CNC strojích, které jsou dalším unikátním prvkem ve výrobním procesu Warwicku, který hned tak každý výrobce nemá. Právě tady dostanou nástroje svůj tvar. „Warwick používá takzvaná pětiosá CNC, zatímco většina ostatních výrobců používá pouze tříosá. Programování je velice složité, ale umožňují nám vyfrézovat i různé náročnější úhly a dovolují v jednom kroku vyrábět i dosti složité tvary nástrojů.“ vysvětluje Irvine. Příkladem jsou například shora i zespodu klenutá těla či příjemně tvarované „patky“ těla pro uchycení šroubovaného krku tak, aby umožnil perfektní přístup do vyšších poloh hmatníku. Zde se pak k uchycení krku používá namísto jednoho kovového plátu čtyř samostatných pouzder s vnitřním závitem pro šroub. A ačkoliv se patka zeštíhluje, hloubka jednotlivých děr pro čtveřici šroubů je naprosto stejná. Moderní CNC stroj se navíc umí přizpůsobit tvaru nástroje tak, že i do zkoseného povrchu dokáže například vyvrtat díry v pravém úhlu k ose těla.
Neviditelné pražce
Zcela samostatnou kapitolou představuje výrobcem používaná unikátní technologie pražcování, momentálně asi největší chlouba celé tovární haly. Na její realizaci pracoval Hans-Peter Wilfer zhruba pět let a v provozu je nyní necelý rok. Procedura přichází na řadu po vyfrézování tvaru krku a hlavy na CNC – výsledkem je sice prakticky hotový krk, ale s dosud neopracovaným hmatníkem.
Jeho následné opracování probíhá v jednom velkém proskleném boxu v řadě navazujících kroků. Tím prvním je vytvarování hmatníku podle příslušného poloměru. Probíhá v šesti fázích v samostatných brousících stupních, takže výsledkem je dokonalý tvar hmatníku. Poté přichází na řadu takzvané neviditelné pražcování. O co vlastně v případě této výrobní fáze jde? „Podíváte-li se na běžný hmatník, můžete snadno vidět, že drážky pro pražce bývají prořezány napříč od kraje ke kraji. Náš přístup je nový v tom, že stroj do hmatníku vyřezává sloty pro jednotlivé pražce tak, že na každé straně ponechává zhruba dva milimetry neprořezané.“ vysvětluje Nina Hoschkara. Následuje osazení pražců s tím, že vše počítačově řídí opět samotný stroj, který se postará i o jejich perfektní zarovnání (leveling). Proces pokračuje nastavením výztuhy a vytvořením postranních značek na hmatníku. Ven vychází hotové krky s dokonale přesnými hmatníky, s jedním jako druhým. „Na každém krku je již předem nalepen QR kód, díky němuž zařízení přesně ví, o jaký model jde, jaký bude poloměr profilu hmatníku, jaké typy pražců má použít a tak dále.“ popisuje možnosti momentálně zřejmě nejmodernějšího výdobytku v oblasti výroby kytar a baskytar Nina. Ačkoliv výrobce mluví o „neviditelných“ pražcích, efekt není zdaleka jen vizuální! „Po obou stranách hmatníku zůstává jeho okraj po celé délce neporušený, což se projevuje jak ve vyšší stabilitě hmatníku, který se díky tomu nemá tendence prohýbat, tak ve vyšším pohodlí při hře. Dokonce i samotné výřezy pro pražce jsou vytvářeny s příslušným zakřivením podle poloměru hmatníku, takže pražce do vzniklých kapsiček perfektně zapadají.“ V praxi, když projedete prsty po stranách hmatníku, jsou naprosto hladké, cítíte pouze dřevo a nezachytáváte o mikronerovnosti, které jsou cítit i při sebedokonalejším začištění pražců. „Oceníte to zejména tehdy, když už hrajete opravdu dlouho.“ dodává Nina.
Povrchová úprava
Právě tady stojí za to zdůraznit propojení mechanického obrábění a práce lidské ruky. Z CNC strojů vycházejí téměř dokonalé, naprosto přesně tvarované nástroje, které vypadají takřka hotově. Je však na zdejších zkušených kytarářích, aby se poté postarali o jemné vybroušení povrchu. Ve třech „kukaních“, umístěných na konci této části výrobní haly, tak tito odborníci trpělivě přebrušují nástroje až do sebemenších záhybů, aby je tak připravili na další podstatnou fázi: povrchovou úpravu.
Přecházíme proto do míst, kde probíhá lakování. Jedná se o další unikum, které je výsledkem vývoje samotného Warwicku. Zákazníci Custom Shopu mají celou řadu možností – od vysoce lesklých laků přes přírodní olej po barevný olej.
Zde narážíme na další výjimečný proces výroby nástrojů Warwick a Framus. K lakování nástrojů zde totiž používají speciální laky na bázi vody. „Je to speciální typ laku, který byl vyvinut přímo tady.“ poznamenává Andy Irvine. „Lak či barvu můžete dokonce vypít a nic se vám nestane.“ povzbuzuje Nina Hoschkara naši vrozenou zvědavost, kterou jsme protentokrát i přes ubezpečení o naprosté ekologičnosti nechali raději přece jen neukojenou. Její slova tak alespoň potvrzuje absence jinde obvyklého agresivního zápachu běžných laků.
K vysoušení laků se používá technologie UV vysoušení. Po nanesení barvy těla nástroje postupně vjíždějí do speciálního boxu, kde je povrchová vrstva kompletně vysušena UV světlem během 10-15 sekund. Tento proces se podle počtu potřebných vrstev opakuje pouze třikrát až pětkrát, takže celková povrchová vrstva je tenčí, zatímco klasického laku je potřeba nanášet až 15 vrstev.
Laky a barvy na bázi vody dokáží zcela nahradit oblíbené nitro laky, ale mají také řadu výhod. Kromě vysoké odolnosti umožňují vytvářet vysoce lesklé povrchy – výsledná vrstva je velmi tenká a naprosto čirá a transparentní, v tomto směru jsou takřka srovnatelné s diamantem. V porovnání s laky na bázi vody se klasické laky při pohledu zblízka jeví spíše mléčné.
Cestou z lakovny jsme narazili také na malou expozici několika desítek druhů dřevin pro custom shop nástroje. Zde je k vidění vzhled žíhaných a obláčkových javorových desek včetně vzácného javoru (jeho kresba působí takřka dojmem 3D), ale i exotických dřev, jako je bahenní jasan, ovangkol, afzelia, mahagon, etimoe, bubinga, ziricote, cocobolo, zebrano a další – zastoupen je prakticky celý svět od Evropy přes Afriku až po Jižní Ameriku. „Když mluvíme o dřevě, situace ve světě je momentálně taková, že začíná být jasné, že některé druhy dřev zkrátka není možné jen nekonečně kácet, vbrzku může dojít i k situaci, že už žádné stromy nezůstanou.“ komentuje Andy. „Někteří z výrobců se už dostali do situace, kdy museli čelit obvinění z nákupu ilegálního dřeva, které nebylo určeno ke kácení. Na druhé straně Hans-Peter s tímto problém nikdy neměl, veškeré dřevo, které tady vidíte, je zcela legální. Nebrání se řídit se selským rozumem a používá i dřeviny, kterých je dostatek.“
Příkladem je využití ebenu na hmatníky – většina výrobců používá pouze ty části, které jsou úplně černé. „Hans-Peter začal používat také eben, který obsahuje světlé pruhy, protože tak může alespoň přispět k záchraně pralesů. Je dokonce levnější, produkujeme tak méně odpadu a přitom nabízí stejnou strukturu i kvality z hlediska tónu. Jeden z výrobců začal nedávno prohlašovat, že zachraňuje prales používáním proužkovaného ebenu, ale Warwick to takto bez velkých slov a kampaní dělá už dvanáct let.“ dodává Irvine. Kromě toho jsme si mohli prohlédnout, jak vypadají nástroje, do nichž se používají efektní LED prvky, například pro osvětlení značek na hmatníku na tmavém pódiu nebo v případě vystaveného signature modelu kytaristy Phila Campbella z Motörhead také pro podsvícení celého loga a tradičního „maskota“ kapely, které jsou ztvárněny na těle.
Zcela odděleně jsou přímo v tovární hale skladovány dýhy pro holow-body kytary v sekci, která je vybavena specializovanými stroji pro výrobu a základní tvarování korpusů a žebrování. Těla jsou poté kompletována ručně s využitím jednoduchých speciálních přípravků pro přesné sestavení korpusu. Poslední oddělení výrobních prostor tvoří několik „kukaní“, kde probíhá kompletace nástrojů a osazení elektronikou – i tu si může zákazník v rámci custom shopu specifikovat podle přání. U baskytar si můžete vybrat mezi elektronikou Bartolini, MEC či Seymour Duncan s různými variantami ekvalizačních prvků. U kytar jsou sériově osazovány především snímače Seymour Duncan, můžete si však vybrat z celé škály produktů včetně aktivní EMG, Di Marzio, klasických P90 a dalších.
Narazili jsme zde například na téměř hotový nástroj – dvoukrkou kombinaci kytary a baskytary – pro basistu kapely Nightwish Marca Hietala. Malou ukázkou preciznosti výroby je, když Nina bere „za krk“ do ruky jednu z nesmontovaných baskytar a zvedá ji do výšky: Kapsa pro šroubovaný krk je vyfrézována tak přesně, že tělo drží naprosto pevně i bez šroubů. To má pochopitelně svůj vliv také na celkový sustain a rezonanci nástroje. Úplně posledním krokem je finální kontrola. Během zhruba dvou hodin určený pracovník důkladně prověří kvalitu každého nástroje a teprve po úspěšném dokončení vypálí na zadní stranu hlavy laserem unikátní sériové číslo. Poté už putuje nástroj pečlivě zabalený v krabici do skladu, kde bude čekat na svoji expedici.
Soběstačný provoz
Stojí za to poznamenat, že veškeré vymoženosti výrobního procesu vlastně vůbec nevznikly s cílem urychlit výrobu – právě naopak. Jak uvedl majitel Warwicku Hans-Peter Wilfer, výroba jednoho nástroje dnes zabere 18 - 30 hodin, zatímco dříve k výrobě baskytary stačilo osm až devět hodin. Celý výrobní proces trvá tři až čtyři týdny. Celkově se zde vyprodukuje maximálně deset baskytar týdně. „Před několika lety jsme přímo zde v Německu produkovali mnohem více baskytar. V posledních letech se zde snažíme soustředit spíše na kvalitu než na kvantitu. Každému kroku věnujeme patřičný čas. Navíc vlastně vůbec neprodukujeme na sklad, nýbrž formou just-in-time, to znamená, že výroba začíná až na základě požadavků.“ vysvětluje Nina Hoschkara.
Za zmínku stojí také přístup Warwicku k životnímu prostředí, ekologii a k nakládání s dřevěným odpadem. Celá hala využívá centrální odsávání prachu a pilin, které je v provozu zhruba rok a odsává odpad ze všech strojů. Výrobce si dává záležet, aby nic nepřišlo nazmar, zejména pokud jde o dřevo, a veškeré odřezky soustředí ve velkém venkovním silu. „Každý kus dřeva se snažíme zužitkovat – pokud se nehodí na tělo či krk, najdeme alespoň pro jeho část jiné využití, a pokud se ani to nepodaří, použijeme jej jako palivo pro topení či chlazení továrny,“ zdůrazňuje Andy Irvine. Ta je podle Andyho zcela soběstačná. „Využíváme solární energii, termální energii i spalování dřeva, nezávisíme na dodávkách energie od kohokoliv jiného. Továrna tak „krmí“ sama sebe a ve skutečnosti dokonce generuje energii, z níž dokonce část dává k dispozici městečku.“
Mimochodem větší kusy dřevěného odpadu byly použity také pro výrobu podlah v kancelářské budově i v přilehlém novém koncertním sále Warwicku, najdete zde díky tomu podlahy či schodiště vyrobené z bubingy a podobně. Důkazem důrazu na životní prostředí jsou také první pokusy o využití dřeva s certifikátem FSC nebo také certifikace EMAS III. Ze všeho je tak patrné především jedno – nejsou to jen plané fráze, je to dobře promyšlená koncepce , kterou je prodchnuto vše, co dnes firma dělá, nebo kam směřuje.
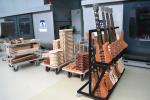
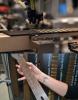
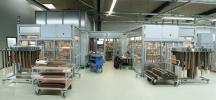